Aflex Metal Expansion joint installation instructions
Aflex – Australia’s only paperless ISO9001:2015 accredited bellows manufacturer
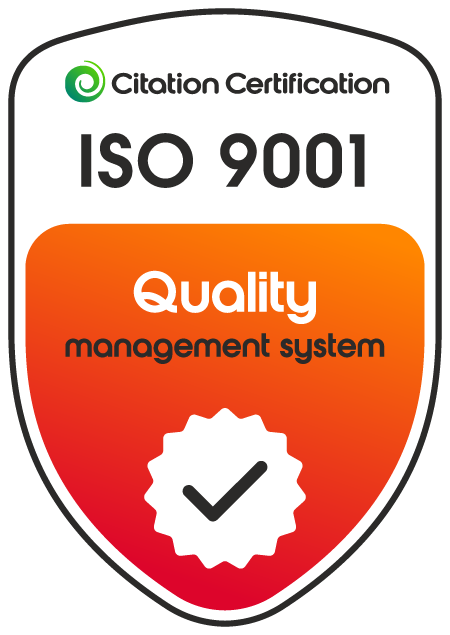
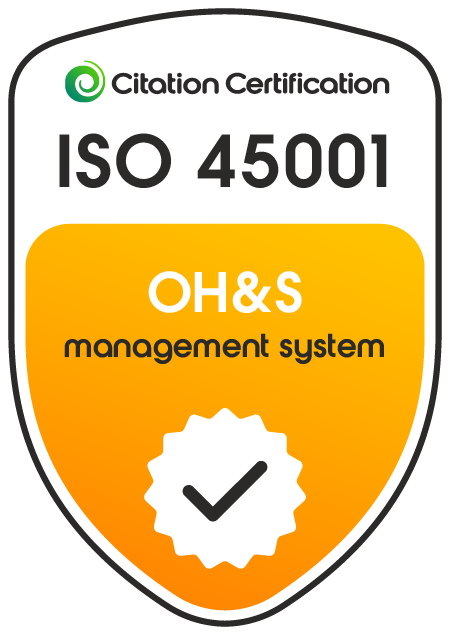
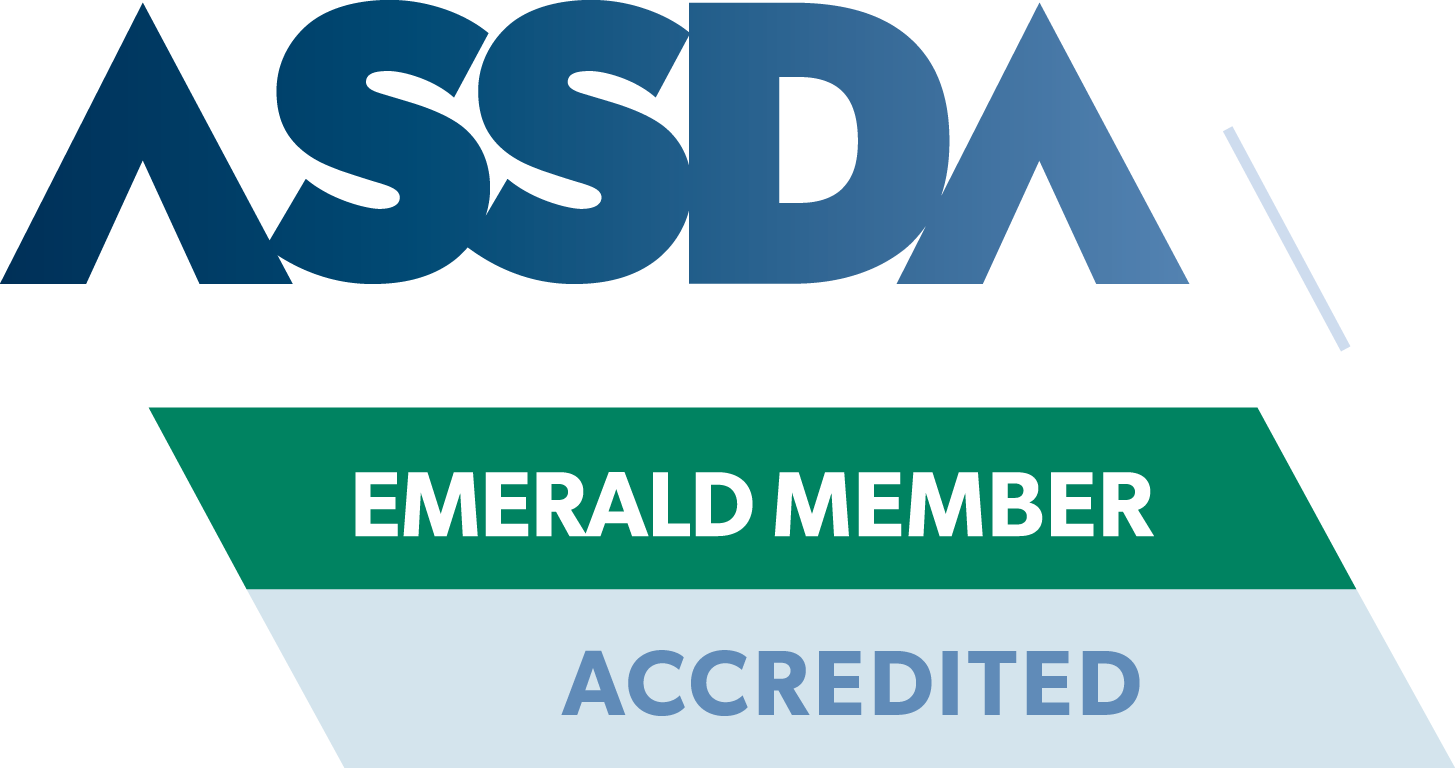
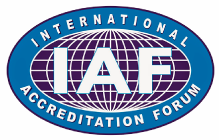
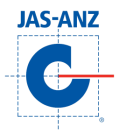
- Before starting the installation process, please verify that the Aflex Serial number plate is securely attached and legible. It’s imperative that the Serial number plate remains attached and accessible in order to maintain positive identification of the bellows assembly. Removing the serial number plate will void the manufacturer’s warranty. The serial number identifies the specific materials, weld procedures, welders and other critical quality data for that item and links to our MDR records. See this link for a sample MDR – Sample MDR
- Verify that the expansion joint is in good condition and free from any damage. This means checking the bellows element itself, the hardware and shipping bars. Sometimes the hardware or shipping bars will be taking a pre-set load, and transit damage could mean the length of the joint has changed. Please notify us immediately if shipping damage is apparent. Any attempt to rectify damage without consultation with the manufacturer will void warranty.
- Ensure that shipping bars (where fitted) are not removed prior to installation. If a shipping bar is causing an installation problem, contact us for advice.
- Welded or pipe end bellows as standard do not have shipping bars. Shipping bars on pipe ends need to be welded directly to the pipe ends which damages the surface coatings on the pipe ends. In the case of bellows with pipe ends, the packing will be suitable so the bellows length is not effected during transport.
- Ensure the gap in the pipe work where the expansion joint is to be installed is the correct size. The pipe work must be made to fit the length and alignment of the joint (unless otherwise specified in the datasheet).
- Always use lifting lugs where provided, or otherwise lift from the hardware parts of the expansion joint. Do not support the weight of the expansion joint from the bellows element itself or from the shipping bars – this can cause damage which will void warranty.
- Ensure that expansion joints fitted with flow liners are installed in the correct orientation. Flow direction is indicated on the shipping bar stickers.
- Ensure any mating flanges are correctly and accurately aligned. Expansion joints subjected to torsion stresses will fail prematurely, and failure due to torsion is not covered by our warranty.
- Once the expansion joint is installed, (whether by bolting or welding) removed the shipping bars. Shipping bars are not designed to restrain pressure thrust and must be removed before site hydro-testing or system pressurisation.
- For unrestrained bellows – SEB, UEB, XB and DXB ensure that the correct anchors and guides are installed as per the EJMA standards guidelines. All unrestrained bellows will exert pressure thrust forces, see this link – Pressure Thrust
- Under no circumstances pressurise the expansion joint to a pressure higher than the ‘Design Pressure’ as listed on the expansion joint datasheet.
- TEB and TUEB assemblies – Click this link for additional specific TEB and TUEB Installation Information.
- Ensure any tie rods are installed prior to service. If the assembly has shipping bars (angle iron with a yellow label) then remove the shipping bars after installation. The Tie Rod arrangement as delivered from the manufacturer must not be removed – the tie rods restrain the pressure thrust during operation. Removal of tie rods can cause bellows and pipeline damage. Deviations or modification will void warranty. Any questions, please don’t hesitate to contact Aflex.
- Flange sealing torques: Aflex do not provide flange bolting torque values. Please refer to the torque values in the relevant flange standard.
- If you have any problems or questions during installation – contact us immediately. We’re here to help, and your feedback is important!